Workplace prosecutions are something that health and safety practitioners, and business leaders should maintain current awareness of. Why? Because you have a legislative duty to acquire and keep up-to-date knowledge of work health and safety matters relevant to the nature of your operations.
In addition, the terminology reasonably practicable, means that you should consider the likelihood and degree of harm a hazard or risk could have. Whilst there may not have previously been an incident at your workplace, if a significant incident has occurred across your industry, it is something you should be aware of.
For the fifth year in a row, Action OHS Consulting has taken some time to collate and review the data available from WorkSafe Victoria and SafeWork NSW.
Used effectively, the provided information should support you to influence key stakeholders within your organisation, and assist your business to make informed decisions with respect to their health and safety program.
This article provides an overview of the prosecutions from 2015 through to the 2019 calendar years.
Prosecutions: Numbers and Related Legislation
Calendar Year 2019 saw a total of 137 prosecutions against the Victorian health and safety legislation, whilst in NSW the number of prosecutions was 37.
***Note at the time when this report was produced, zero (0) prosecution had been listed on the SafeWork NSW website – should this change, this report will be updated accordingly***
When compared to the previous year, there has been a 4% increase in Victoria and a 22% decrease in NSW. With respect to NSW, the prosecution in the current calendar year, align with the number of prosecutions in calendar year 2016 and 2017 where there were 35 and 27 prosecutions respectively.
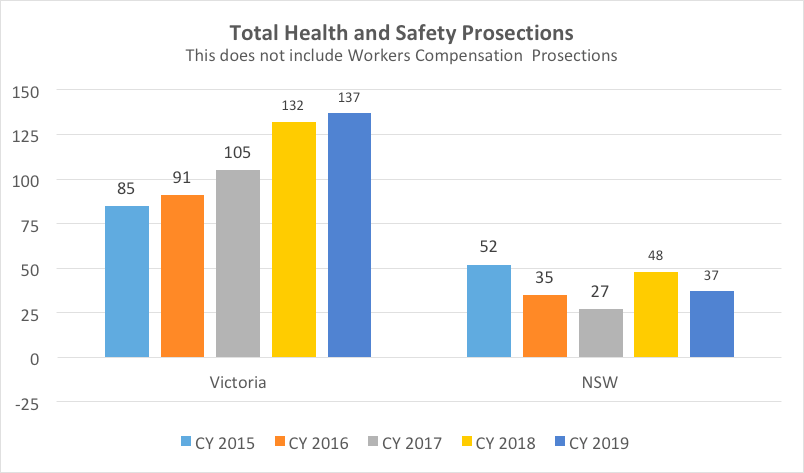
Within Victoria:
- 121 prosecutions were recorded against the Occupational Health and Safety Act 2004 only
- 1 prosecution was recorded against the Occupational Health and Safety Regulations 2017 only
- 15 prosecutions involved both the Occupational Health and Safety Act 2004 and the Occupational Health and Safety Regulations 2017
- Unlike previous years, no prosecution involved the Dangerous Goods Legislation.
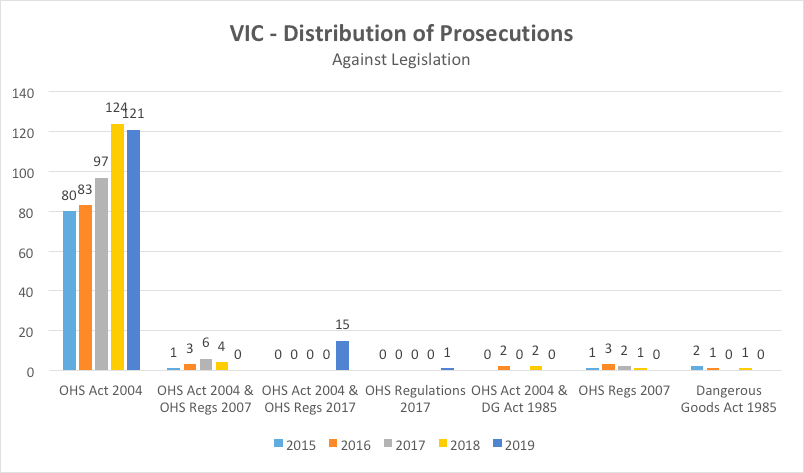
Zero prosecutions were against the 2007 version of the Occupational Health and Safety Regulations which were updated in 2017.
Within NSW:
- 34 prosecutions were recorded against the Work Health and Safety Act 2011 only
- 2 prosecution was recorded against the Work Health and Safety Regulation 2017 only
- 1 prosecution involved both the Work Health and Safety Act 2011 and the Work Health and Safety Regulation 2017
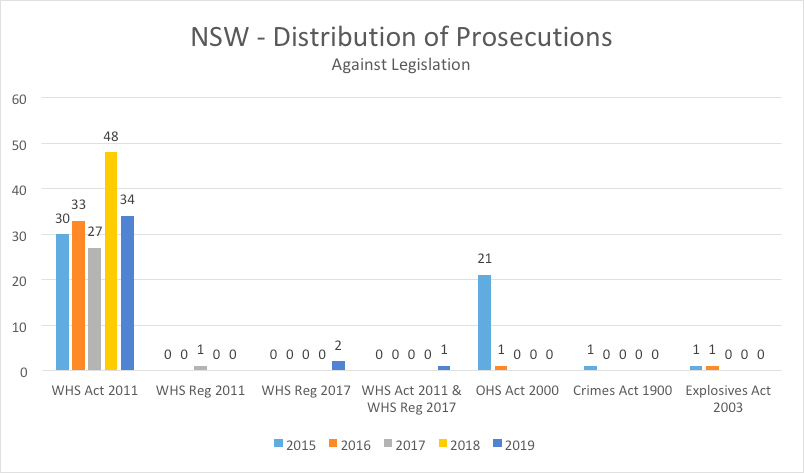
Following the last prosecution against the Occupational Health and Safety Act 2000 being in 2016, and with their being no prosecutions since 2017, this signals a complete transition in NSW to prosecutions against the harmonised legislation.
Note the Occupational Health and Safety Act 2000 was superseded as of 1 January 2012.
Prosecution Timeframes
The timeframe for the prosecution’s outcomes from 2018, when measured against the date of the offence have been listed in the table below.
Table 1: Timeframe between date of offence and the prosecution outcome, for the 2018 prosecution outcomes reported by SafeWork NSW & WorkSafe Victoria. Bracketed numbers represent the increase / decrease from 2017.
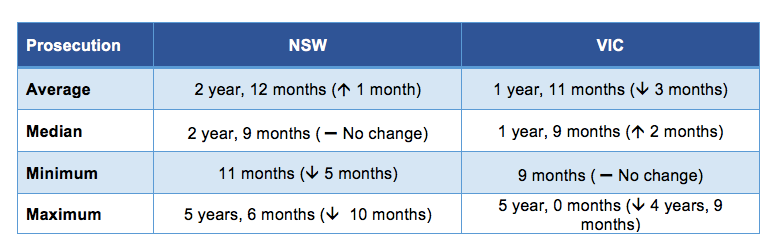
Health and Safety Fines
Year on year, the average fine and median fine decreased in Victoria, and increased in NSW. In Victoria the median fine has been relatively stable over the last 5 years. The average and median fines were greater in NSW, when compared to Victoria. However, there were approximately 4 times more prosecutions in Victoria, compared to NSW.
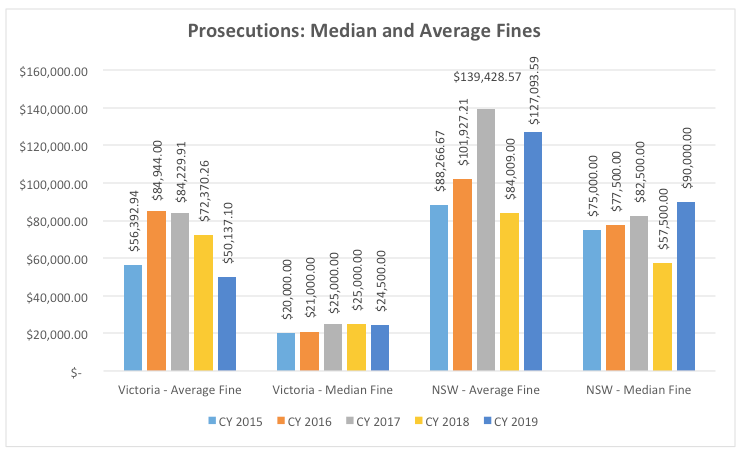
In NSW each prosecution resulted in a monetary fine. In Victoria 124 fines were issued (91% of prosecutions).
In addition to the fines, WorkSafe Victoria issued 8 Enforceable Undertakings in 2019 which equates to 6% of prosecutions. This is compared to the 6 (7%), 7 (8%), 10 (7%) and 6 (5%) Enforceable Undertaking issued in 2015, 2016, 2017 and 2018 respectively. An enforceable undertaking is a legally binding agreement between WorkSafe Victoria and the employer. The employer is obliged to carry out the specific activities outlined in the agreed undertaking. EU’s will typically guide and direct the business being prosecuted to improve its health and safety program.
Health and Safety Fines: Maximum Issued
With respect to fines, the maximum fines for both Victoria and NSW decreased year on year.

The maximum fines issued to a business were associated with the following events:
- Victoria: Bradken made heavy metal components by casting. The castings weighed between 200 and 270 kg and were used in mining, excavation and transport. On 22 July 2014 the castings being manufactured were end blocks for excavators. The manufacturing process commenced with moulds being formed with sand and chemically bonded to make the block. The leading hand then made a core to go inside each mould (to create cavities), and the mould was then placed on a line (like a miniature railway) to move the moulds into the furnace. Inside the furnace molten metal was heated to about 1580° Celsius. The metal was poured into each mould. Each end block casting weighted approximately 270kg at pour; the casting and mould together weighed about 800–900kg. A pneumatic arm pushed the mould along the line and the mould with the castings still inside was left for approximately two hours to cool. After about two hours, the casting was removed from the sand mould. The casting was taken to a cooling bin and the sand was removed from the area and stockpiled to be on-sold for roadmaking. At the time of the incident, the castings were moved using a skid steer loader which had been used in this procedure since its purchase in June 2012. The windscreen of the skid steer loader was fitted with 6mm toughened glass, with an industrial film placed over the outside. Mr. Watson was tasked with removing the castings from the mould and then placing the casting in the cooling bin. This process was known as “knocking out” ie knocking out the castings from the sand moulds. The process also included “knocking off” any remaining sand. The process was undertaken by an employee using the skid steer loader. The mould was tipped off the conveyor onto the concrete floor. The casting temperature was still (on average) about 580°C at this time. The tipping process usually broke the mould from around the casting; otherwise the skid steer operator was required to use the lip of the bucket to break the mould. The operator then picked up the casting using the bucket of the skid steer loader, knocked off any remaining sand, and moved the casting to the cooling bin. There were no eyewitnesses to the event which led to Mr. Watson’s death. A fellow Bradken employee saw the skid steer loader on fire about 100 metres from where he was working. When he ran over he saw Mr. Watson was seated in the cabin of the loader and the casting was resting on him. Mr. Watson was not moving and was charred by the fire. Police and paramedics attended the scene. It took a considerable time for the fire to be extinguished and the casting to cool sufficiently to allow access to Mr. Watson’s body. The cause of death was recorded as “effects of fire”.
- NSW: On 25 October 2016, a 55-year-old carpenter suffered fatal injuries when he fell from the exposed edge of a partially constructed formwork deck under construction and was impaled through the chest on a reo bar, at Ryde. After a SafeWork NSW investigation, the defendant, Truslan Constructions Pty Ltd, was charged with a breach of section 32/19(1) of the Work Health and Safety Act 2011. On 12 July 2019, the defendant was convicted by the District Court and fined $450,000
It is not just businesses that are being prosecuted in relation to health and safety breaches
If you were of the understanding that health and safety prosecutions were limited to corporations – think again. In 2019, 13% and 19% of prosecutions were issued to workers in Victoria and NSW respectively – equating to 18 and 7 prosecutions respectively.

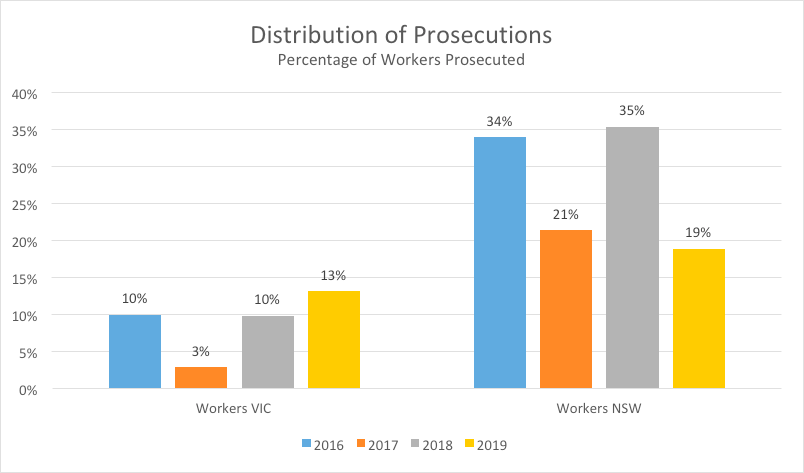
Prosecutions: What is the Cause and where are the Gaps?
With respect to the criteria/codes that lead to the prosecution – the criteria that was associated with 10% of the prosecutions in 2018, as defined by WorkSafe Victoria, are outlined below.
These criteria are relatively consitent since 2015. In 2019 there was an increase in “guarding-related” prosections, highlighted by the increase in “Guarding”, “Unguarded plant” along with the “Failure to provde and maintain plant”.
“Failure to provide a safe system of work” continues to places a clear duty on all workplaces to understand their operations, the hazards associated with their work, and ensure that the established controls are implmented.
Other criteria noteworthy to report on includes reductions in prosecutions related to failure to conduct risk/hazard identification or risk assessment:
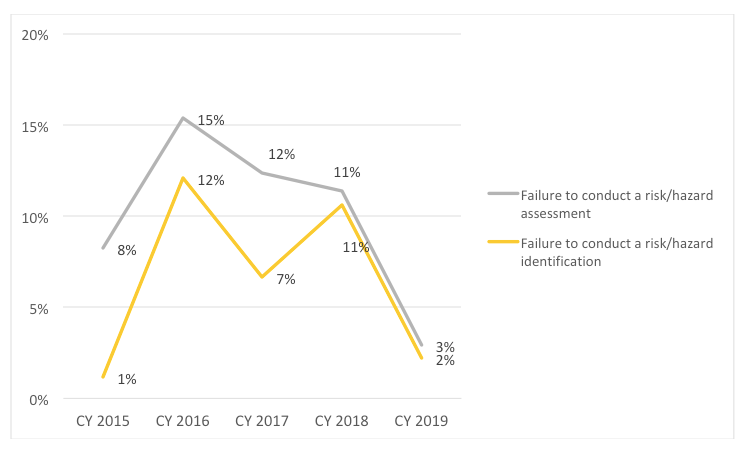
The Complimentary Support
Action OHS Consulting continues to observe a rise in inbound calls for support, associated with businesses wanting guidance, on how they can best manage their legal obligations associated with health and safety.
Action OHS Consulting is on a panel of providers endorsed by WorkSafe Victoria which provides complementary OHS Review’s for Victorian-based businesses with less than 60 workers across a period of 12-months. If you would like to find out more about this program, please contact us – Contact Us.
The Takeaway
Due diligence is all about collecting information to better understand health and safety impacts associated with a business’s operation, to allow better and more informed decisions being made.
The intention; is to protect workers, contractors, customers and visitors from harm. It is the duty that is placed on senior managers and businesses under the health and safety legislation, and their for is a duty that all businesses must be aware of.
With respect to the Health and Safety Legislation, it adopts a risk-based approach. This means that business and their senior managers are required businesses to understand and manage the hazards associated with their operations (due diligence). Put simply, this leads to a requirement for workplaces to actively:
- Ensure that your safety program easy to access and understand, and importantly relevant to your operations. Strongly consider implementing safety software such as Safety Champion, to help ensure that scheduled tasks are completed, and that workers can easily report incidents and/or hazards. Ensuring that you have visibility and read access to this information, will assist you to proactively prevent incidents from occurring in the future.
- List all the ways your workers could get hurt, and document what you have put in place to stop this from happening. Start by listing the “Top 5” hazards – focusing on those which could cause the most serious harm. Do this in consultation with a selection of workers who hold different roles within your business. If you identify things that you could improve and/or do better, this is not bad, in fact, it is the point of the exercise.
- Continue to consult. Have regular structured and unstructured conversations with your team regarding the controls you have established.
- Build competency. Ensure that you have an induction program that includes an overview of your safety program and the operational activities that the worker will undertake. Consider assigning a “buddy” to “new” and/or “young” workers.
- Ensure your safety program is sustainable. Don’t rely on just one person. Spreadsheets and folders can be effective if you are organised, however, are difficult to maintain visibility when tasks are due – or more importantly, when tasks are missed. Software programs like Safety Champion Software will support visibility of your health and safety program, guide and remind you when deadlines and key milestones approach.
- Considering safety when engaging contractors. Workplaces often engage contractors to support processes that the workplace is not familiar with, which often means new hazards are introduced to the workplace. Prior to engaging contractors, along with price, seek information from the contract to understand how they will help you maintain a safe working environment when they are onsite.
- Consider safety as part of your procurement process. Before you buy anything, consider the safety implications. Don’t limit this to equipment, machinery, computers – extended this to services as well. Don’t make safety an afterthought.
We would be interested to hear your thoughts, questions or fears.
If, like us, you would like to interrogate data, we would be more than happy to share an unlocked copy of the data with you – simply Contact Us.